Unlocking the Power of Precision Injection Molding Suppliers
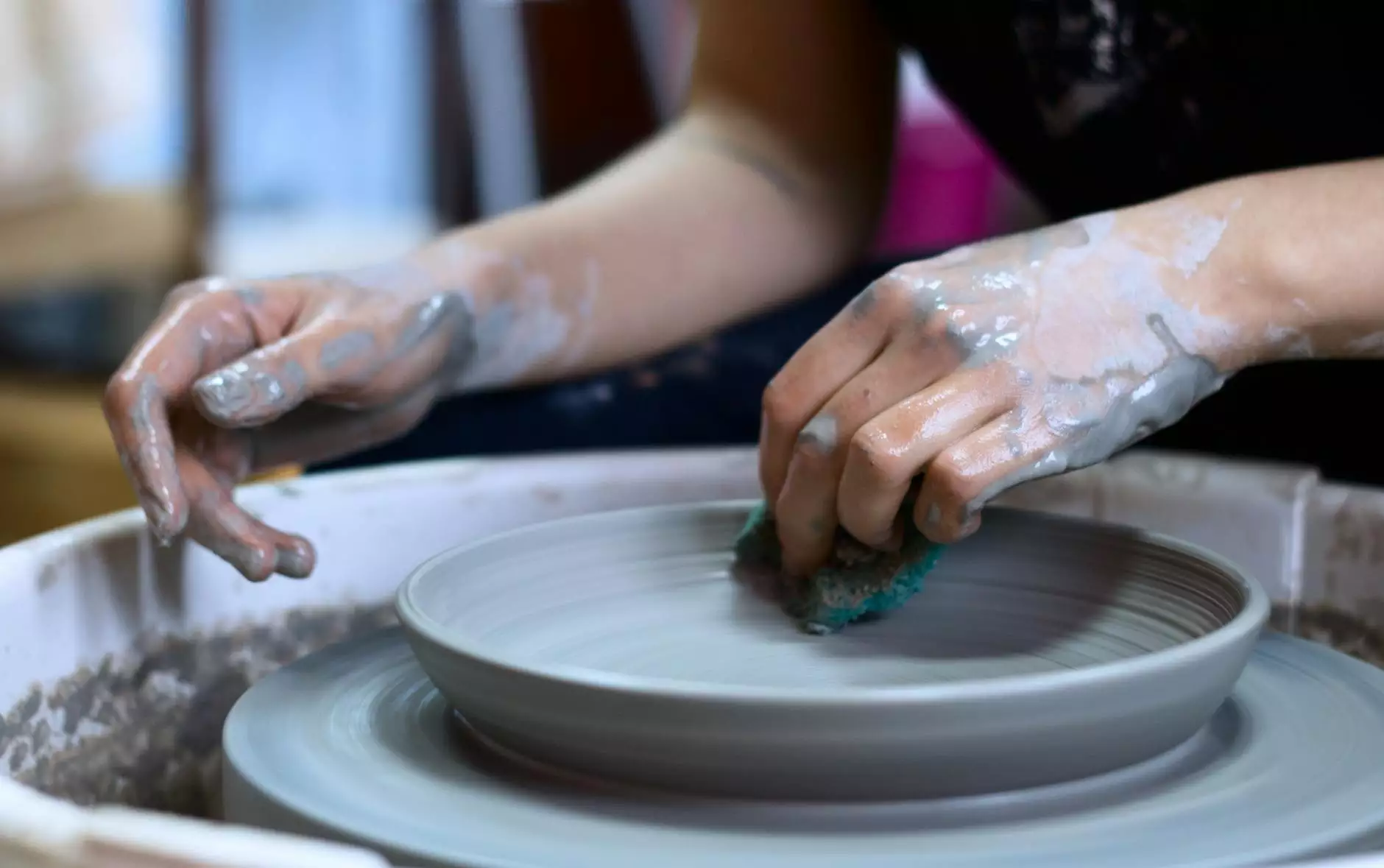
The manufacturing industry has evolved tremendously in recent years, driven by technological advancements and the growing demand for highly precise and efficient production processes. In this context, precision injection molding suppliers emerge as pivotal players, providing essential services that cater to a wide array of industries, including automotive, medical, consumer products, and more. In this article, we will delve deep into the world of precision injection molding, exploring its significance, benefits, processes, and how these suppliers operate to deliver exceptional results.
Understanding Precision Injection Molding
Precision injection molding is a highly sophisticated manufacturing process that involves injecting molten plastic or metal into a mold to create detailed and accurate components. This method is not just about producing items; it is about ensuring that every component meets stringent quality standards while being produced in a cost-effective and timely manner.
The Importance of Precision in Manufacturing
In the realm of manufacturing, precision is synonymous with quality and reliability. Tighter tolerances and intricate designs are increasingly becoming the norm, necessitating the expertise of precision injection molding suppliers who can deliver on these demands. Let’s explore several reasons why precision is crucial in manufacturing:
- Enhanced Product Quality: Precision molding ensures that every component meets exact specifications, which is critical for products requiring high reliability, such as those used in the medical and automotive sectors.
- Reduced Waste: High precision leads to fewer defects, significantly lowering waste and ultimately reducing production costs.
- Increased Efficiency: Well-engineered molds and processes allow for quicker production cycles, enabling businesses to respond faster to market demands.
- Improved Customer Satisfaction: Delivering high-quality products on time leads to increased customer trust and satisfaction, which is vital for long-term business relationships.
Key Benefits of Working with Precision Injection Molding Suppliers
The value that precision injection molding suppliers bring to the table extends far beyond the manufacturing process itself. Here are some key advantages:
1. Expertise and Experience
Partnering with skilled suppliers gives businesses access to a wealth of knowledge and experience. These suppliers understand the nuances of various materials and can recommend the best options for specific applications.
2. State-of-the-Art Technology
Leading precision injection molding suppliers invest heavily in cutting-edge technologies, including:
- 3D Printing for rapid prototyping
- Advanced CNC machining
- Automated quality control systems
This investment allows them to produce parts with unmatched precision and consistency.
3. Custom Solutions
Every project is unique, and the best suppliers offer tailored solutions to meet specific client needs. They can design molds that meet exacting specifications and provide ongoing support throughout the production process.
4. Cost-Effectiveness
Although precision molding may have higher initial costs, the long-term savings from reduced waste, improved quality, and faster production times can lead to significant cost benefits.
5. Scalability
As businesses grow, their manufacturing needs may change. A reliable precision injection molding supplier can scale production seamlessly to accommodate increases in demand, ensuring that businesses can grow without disruptions.
The Process of Precision Injection Molding
Understanding the process behind precision injection molding is vital for appreciating its benefits. Here’s a breakdown of the key steps involved in the process:
1. Design and Prototyping
The journey begins with design. Engineers work closely with clients to create 3D models that reflect the desired specifications. Prototyping allows for testing and refinement before full-scale production begins.
2. Mold Fabrication
Once the design is approved, the next step is to create the mold. This is a critical phase where precision is paramount, as imperfections in the mold can lead to defects in the final product.
3. Material Selection
The choice of material greatly influences the final product's characteristics. Precision injection molding suppliers often offer a range of materials, including various plastics and metals, tailored for specific applications.
4. Injection and Cooling
The molten material is injected into the mold under high pressure. Once the material has filled the mold, it is allowed to cool and solidify, forming the desired part.
5. Quality Inspection
After cooling, each part undergoes rigorous quality inspections using advanced technologies to ensure compliance with the specified tolerances and quality standards.
6. Finishing Touches
Finally, any finishing work such as painting, coating, or assembly is performed to meet the final product specifications.
Emerging Trends in Precision Injection Molding
The precision injection molding industry is continually evolving, influenced by technological innovations and market demands. Here are some emerging trends:
1. Sustainability Initiatives
With increasing awareness of environmental issues, many precision injection molding suppliers are investing in sustainable practices, including the use of recycled materials and energy-efficient processes.
2. Smart Manufacturing
The integration of smart technology, including IoT (Internet of Things) and AI (Artificial Intelligence), enables real-time monitoring and analytics of the manufacturing process, enhancing efficiency and enabling predictive maintenance.
3. Advanced Materials
Developments in material science have led to the emergence of advanced polymers and composites that offer superior performance characteristics, such as weight reduction or improved heat resistance.
Choosing the Right Precision Injection Molding Supplier
When selecting a precision injection molding supplier, it’s essential to consider several factors to ensure a successful partnership:
1. Experience and Reputation
Look for suppliers with a proven track record in your industry. Client testimonials and case studies can provide valuable insights into their capabilities.
2. Capabilities and Services
Assess the range of services offered. A supplier that provides additional services such as design consultation, prototyping, and logistics can be a valuable partner.
3. Quality Standards
Ensure that the supplier adheres to recognized quality standards such as ISO certification. This adherence indicates a commitment to quality and continuous improvement.
4. Communication and Support
Effective communication is critical for successful collaboration. Choose a supplier who is responsive and willing to engage throughout the process.
5. Pricing Structure
While cost should not be the sole determining factor, it is essential to evaluate pricing relative to the quality of services provided. Look for transparency in quotes and avoid hidden fees.
Conclusion
In the dynamic landscape of modern manufacturing, partnering with the right precision injection molding supplier can significantly affect a business's success. These suppliers are not merely vendors; they are strategic partners that can enhance product quality, efficiency, and innovation. By understanding the benefits and intricacies of precision injection molding, businesses can make informed choices that drive growth and competitiveness in their respective markets. At deepmould.net, we pride ourselves on being at the forefront of injection molding technology, ready to support your manufacturing needs with precision and expertise.