Maximize Your Manufacturing Efficiency with Premium Silicone Membrane for Vacuum Forming
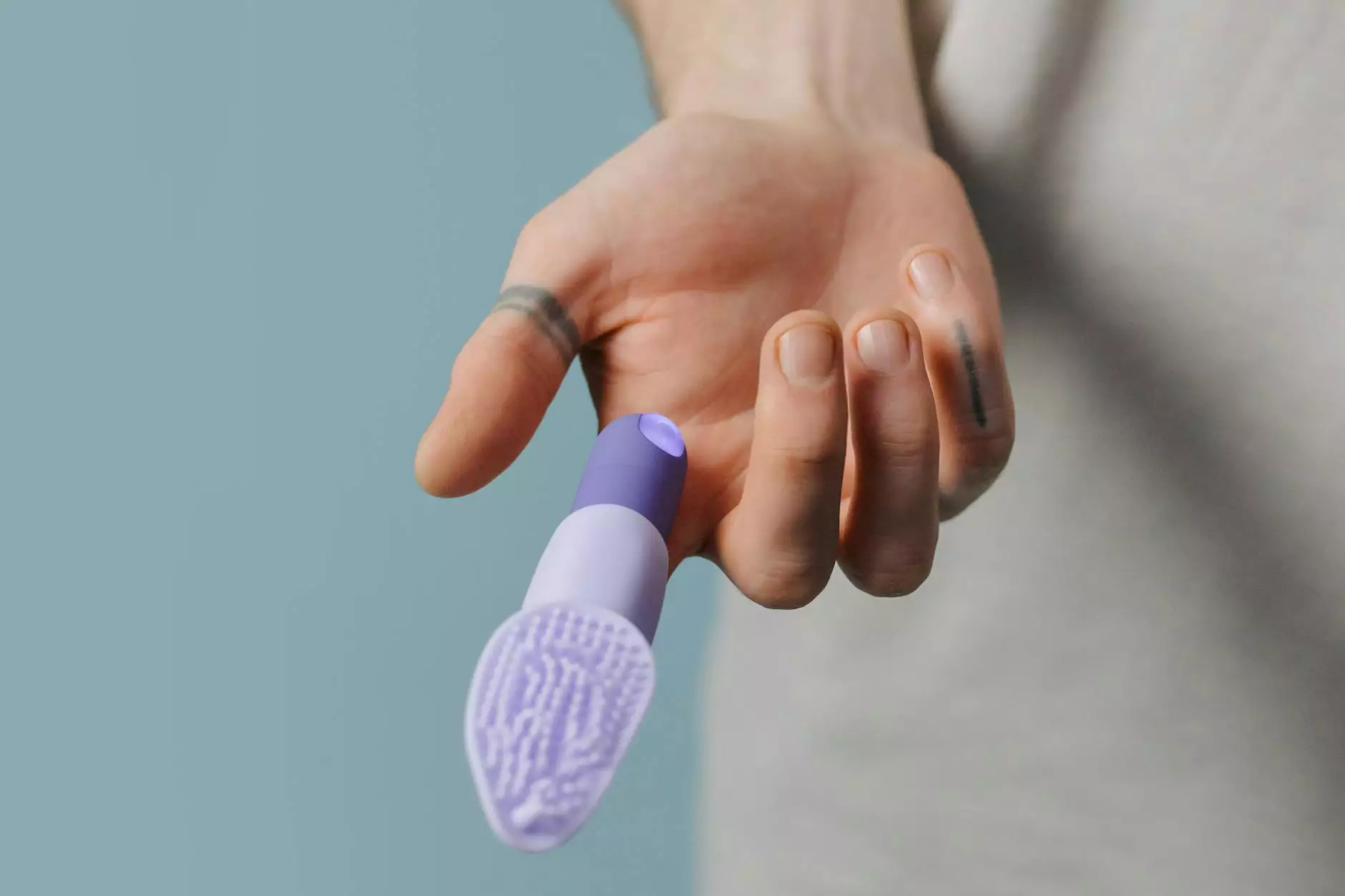
In the rapidly evolving world of manufacturing, innovative materials play a crucial role in enhancing productivity, product quality, and operational efficiency. Among these materials, the silicone membrane for vacuum forming stands out as a transformative solution, offering unparalleled benefits for industries ranging from packaging to aerospace. When selecting a silicone membrane, it’s vital to understand its unique properties, applications, and the advantages it brings to your production line.
Understanding the Role of Silicone Membranes in Vacuum Forming
Vacuum forming is a versatile and widely used thermoforming process that involves heating a plastic sheet and then molding it onto a pattern or a mold using vacuum pressure. The silicone membrane acts as a critical component in this process, serving as a flexible, durable, and heat-resistant interface that ensures precise and consistent molding results.
Unlike traditional materials, the silicone membrane for vacuum forming provides excellent thermal stability, allowing it to withstand high temperatures without degradation. Its flexibility ensures it can conform to complex molds, while its chemical inertness guarantees long-lasting performance in demanding industrial environments.
Why Choose Silicone Membranes for Vacuum Forming?
- Exceptional Heat Resistance: Silicone membranes operate efficiently at temperatures ranging from -60°C to +250°C, making them ideal for high-temperature applications involved in vacuum forming.
- Superior Flexibility and Conformity: They conform to intricate mold geometries, ensuring uniform pressure distribution and precise replication of details.
- Durability and Longevity: Silicone membranes resist mechanical fatigue, tears, and weathering, providing extended service life and reducing replacement costs.
- Non-Stick Surface: The inherent non-stick property facilitates easy removal of formed parts, minimizing defects and clean-up time.
- Chemical Inertness: Resistance to oils, solvents, and other chemicals used during manufacturing enhances operational reliability.
Applications of Silicone Membranes in Modern Manufacturing
The versatility of silicone membranes for vacuum forming makes them suitable across a broad spectrum of industries:
- Packaging Industry: Forming complex plastic shapes for food containers, medical packages, and consumer goods.
- Aerospace: Manufacturing lightweight, high-precision components with intricate geometries.
- Automotive: Producing custom instrument panels, interior panels, and trim components.
- Medical Devices: Creating biocompatible, sterile forms for medical equipment and disposables.
- Art and Design: Crafting detailed prototypes and artistic sculptures with high fidelity.
Advantages of Investing in High-Quality Silicone Membranes
Choosing the right silicone membrane is crucial for optimizing vacuum forming processes. Here are some of the key advantages:
- Enhanced Production Efficiency: Faster cycle times due to superior thermal conductivity and quick recovery from deformation.
- Consistent Quality: Reproducibility of intricate details with minimal defects, ensuring customer satisfaction.
- Cost Savings: Long lifespan reduces replacement costs; non-stick properties minimize cleanup and waste.
- Environmental Benefits: Silicone's inert nature reduces the need for harsh cleaning chemicals, promoting greener manufacturing practices.
How to Select the Right Silicone Membrane for Your Business
Not all silicone membranes are created equal. To maximize benefits, consider the following factors:
- Thickness and Fabrication: Choose an optimal thickness based on your application for balance between flexibility and durability.
- Temperature Range: Ensure the membrane can handle the maximum operating temperatures in your process.
- Surface Finish: A smooth, non-porous surface enhances release properties and part quality.
- Chemical Compatibility: Confirm resistance to any chemicals or vapors used during forming.
- Custom vs. Standard Sizes: Determine whether a tailored solution is necessary to fit your mold dimensions.
Quality Assurance and Maintenance of Silicone Membranes
To preserve the integrity and lifespan of your silicone membrane for vacuum forming, implement regular maintenance protocols:
- Routine Inspection: Check for signs of wear, tears, or delamination.
- Cleaning: Use mild, silicone-safe cleaning agents to remove residues without damaging the surface.
- Proper Handling: Avoid sharp objects and excessive stretching during installation or removal.
- Storage: Keep in a cool, dry environment away from direct sunlight and ozone exposure.
- Replacement Schedule: Based on operational hours and wear, plan timely replacements to prevent process disruptions.
Comparing Silicone Membranes to Other Materials
While rubber membranes and natural rubber membranes are also used in vacuum systems, silicone membranes offer distinct benefits:
FeatureSilicone MembranesRubber MembranesNatural Rubber MembranesTemperature ToleranceUp to +250°CTypically lower, around +80°C to +150°CLimited to +70°C to +110°CDurabilityHigh resistance to mechanical stress and agingModerate, prone to cracking over timeLess resistant to ozone and environmental factorsChemical ResistanceExcellent, inert to many chemicalsVariable, limited chemical resistancePoor, susceptible to oils and solventsFlexibility & ConformityExcellent, ideal for complex moldsGood but less conformable with intricate detailsModerate, limited flexibilityPartnering with vacuum-presses.com for Your Silicone Membrane Needs
As a leading provider in the industry, vacuum-presses.com offers a comprehensive range of buy membranes, including premium silicone membranes, rubber membranes, and natural rubber membranes. Their expertise ensures you receive products that meet the highest standards of quality, reliability, and performance.
Benefits of choosing vacuum-presses.com include:
- Custom Solutions: Tailored membranes designed precisely to your specifications.
- Bulk Purchasing Options: Cost-effective packages for large-scale manufacturing.
- Technical Support: Expert guidance on selecting and maintaining your membranes.
- Fast Delivery: Prompt fulfillment to minimize downtime.
- Comprehensive Product Range: All necessary vacuum system parts for seamless integration.
Investing in the Future: Innovations in Silicone Membrane Technology
The field of silicone membrane technology continues to advance, focusing on enhancing durability, environmental sustainability, and manufacturing precision. Emerging innovations include:
- Nanostructured Surfaces: Improving non-stick properties and reducing release times.
- Hybrid Materials: Combining silicone with other polymers for enhanced performance.
- Eco-Friendly Formulations: Developing biodegradable and ozone-resistant membranes.
- Smart Membranes: Incorporating sensors for real-time monitoring and performance tracking.
Summary: Unlocking the Full Potential of Your Vacuum Forming Processes
In the competitive landscape of manufacturing, leveraging advanced materials like silicone membrane for vacuum forming can deliver significant advantages. From increased precision and process efficiency to long-term savings and environmental benefits, the right silicone membrane is an investment that pays dividends.
Partner with experienced suppliers like vacuum-presses.com to access high-quality, customizable membranes and support that ensures your production stays ahead of the curve.
Conclusion: Elevate Your Manufacturing with Superior Silicone Membranes
Adopting silicone membranes in your vacuum forming operations unlocks new levels of performance, reliability, and product quality. Embrace this innovative material today and experience the transformative impact it can have on your manufacturing processes and business success.
Contact vacuum-presses.com now to explore our extensive range of buy membranes, rubber membranes, and vacuum system parts — your gateway to efficient, high-precision manufacturing.